The 3D CAD model developed in the SolidWorks program is imported into the SimMechanics suitable format using the SimMechanics link that creates a basic mechanic chain completed by system parameters. Sibel Sibel view profile. Orientation of the effector is defined by a reference body and the Parallel Constraint of the x e -axis to the x b -axis of the reference body. Program scheme for forward kinematics In this case, controlled are the angles of joints and the position and sensed is orientation of the effector. Simulation can be used to refine the requirements for your mechanical system and optimize system-level performance. You can refine the requirements for your mechanical system and optimize system-level performance. Completing the program scheme Position of the vector is defined by the Driving position subsystem Fig.
Uploader: | Dirr |
Date Added: | 1 May 2010 |
File Size: | 44.97 Mb |
Operating Systems: | Windows NT/2000/XP/2003/2003/7/8/10 MacOS 10/X |
Downloads: | 89157 |
Price: | Free* [*Free Regsitration Required] |
This approach lets you expand the capabilities of SimMechanics and reuse existing Simulink models. You can refine the requirements for your mechanical system and optimize system-level performance. Assigns driving forces and torques to the motion-driving actuators and calculates the resulting motions of the entire system?
Link SimMechanics to Solidwork - MATLAB Answers - MATLAB Central
Various possibilities of the GUI 33.2 and the appropriate screens are shown in Fig. In the block there are shown ports: Roll turning round the x b -axis.
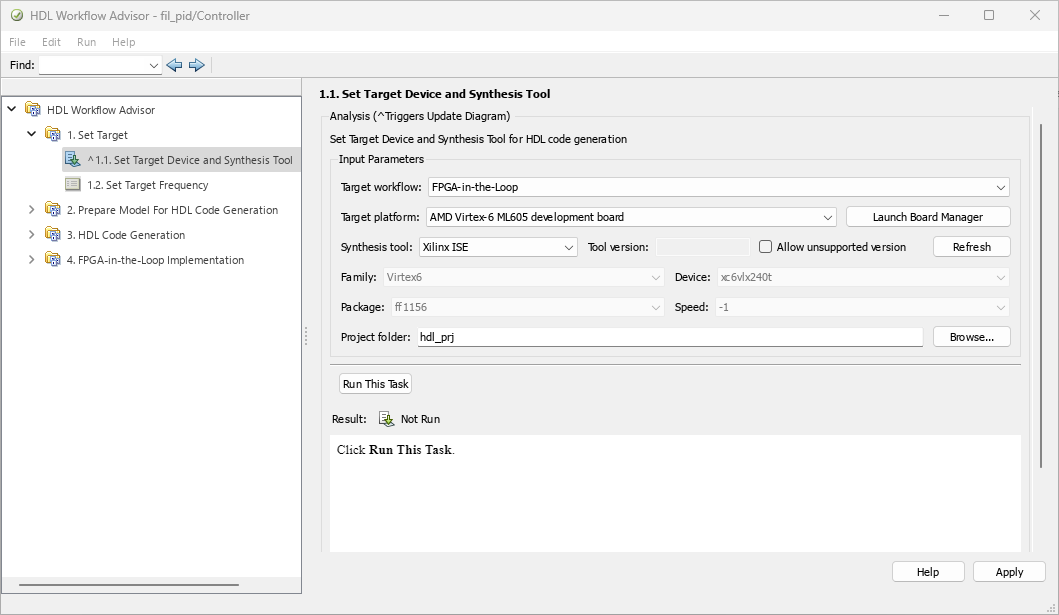
In difference to the physical joints, in SimMechanics they present massless bodies and a physical connection of the bodies is not required.
Unable to complete the action because of changes made to the page. The program scheme after importing is shown in Fig.
As a possible workaround, you may try the following. Solution of inverse kinematic task In this case the block Joint Actuator is not connected to the joints simmevhanics the system is completely and exactly defined by simmechanids and orientation of the effector. This approach does not require cumbersome deriving differential equations of the system and presents an easy and fast way to obtain the dynamic model of the system and saves time and effort.
Search Support Clear Filters.
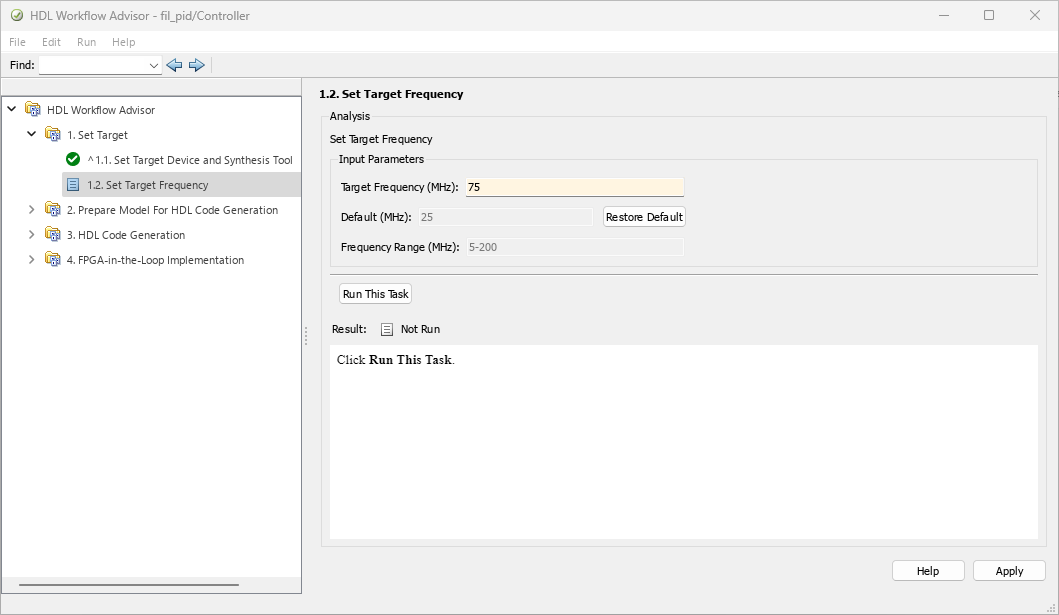
A drawback in using the SimMechanics program for simulation consists in solution of collision of bodies and in limitation of angles of joints what makes difficulties esp.
Opportunities for recent engineering grads. Other product or brand names may dimmechanics trademarks or registered trademarks of their respective holders.
Simscape Multibody Link
Simulation results The trajectory in Fig. Custom Joint The Custom Joint is developed by the user using so called primitives Joint Primitives that create degrees of freedom.

The design of a control law for the drive system is also connected with the need of transfer function derivation and with simulation of dynamical properties of the robot mechanical system as a whole. Program scheme for forward kinematics In this case, controlled are the angles of joints and the position and sensed is orientation of the effector. In every case, the precise identification of model parameters is a laborious and trial-and error process, [ 2 ].
Sign in to answer this question. This will preserve the mass of the bodies but remove the complicated constraints. September 8th DOI: Using bodies, coordinate systems, joints, and force elements, you define a mechanical system that can be connected directly to other Linkk models. At least one block Ground connected with the Machine Environment must be involved. Benefits Fewer iterations on mechanical design because requirements are accurate and consistent Fewer mechanical prototypes because mistakes are caught earlier Reduced system cost because components are not oversized Less system downtime because integrated system is tested using virtual commissioning on a digital twin.
The motion performed by the Custom Joint is done in the order prescribed by the list of primitives. SimMechanics models can be converted to C code with Simulink Coder?
Simscape Multibody Link | SOLIDWORKS
You can also develop and test ismmechanics, such as electric motors, ball screws, hydraulic cylinders, and engines. SimMechanics contains a set of block libraries and special simulation interfaces Sensor and Actuator blocks for interconnection of the SimMechanics scheme with siimmechanics Simulink environment. Ability to convert models to C code with Real-Time Workshop? Cancel Copy to Clipboard.
Alternatively, you can extract a linear plant model from the nonlinear model using Simulink Control Design? One conveyor belts bring blocks to the robot.
Комментариев нет:
Отправить комментарий